Guida alla produzione di serigrafia per circuiti stampati
Guida alla produzione di serigrafia per circuiti stampati
In printed circuit board, copper clad laminate is widely used. In addition to drilling, hole metallization and circuit electroplating, the manufacturing process of double panel is basically the same as that of single side laminate. After cutting, surface treatment, drilling, hole metallization, copper plating and screen printing.
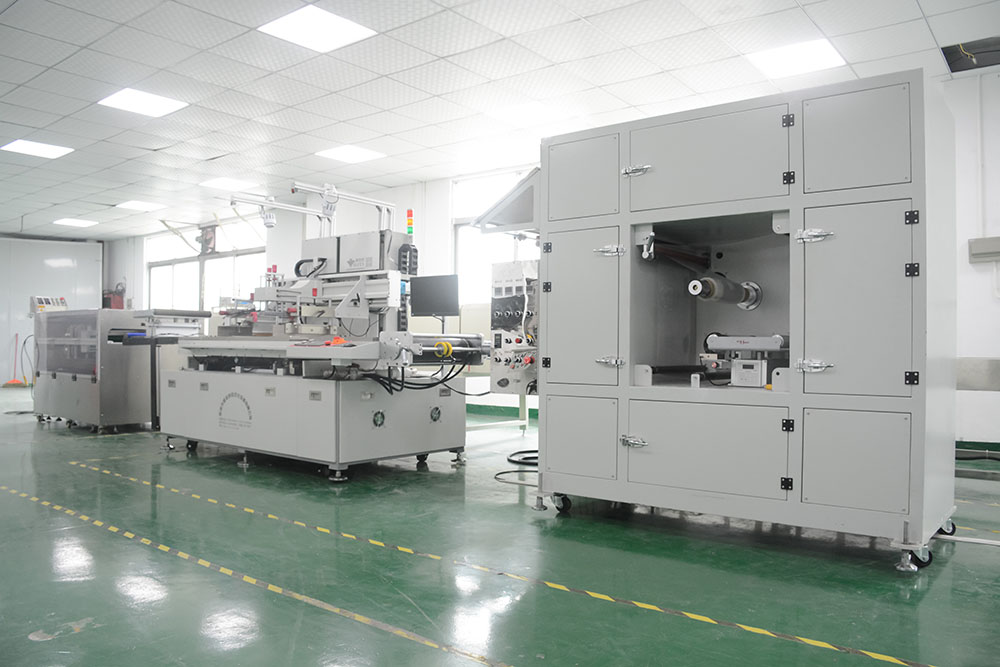
Roll to Roll Flat Bed Silk Screen Printing Machine
1) Screen making is the key to screen printing of circuit board.
It is necessary to use screen, screen frame and photosensitive materials correctly. Screen control ink flow, printing thickness and determine the durability of screen. Generally, high tension, monofilament, plain woven polyester polyester wire mesh or stainless steel wire mesh should be selected. In addition, the new screen should be roughened and degreased to ensure the quality of the mesh plate and prolong the service life of the screen. High tension aluminum mesh frame is generally selected, and the quality is ideal. It is very important to pay attention to the adjustment and control of tension. The net frame that has been stretched should stay on the tension machine for more than 48 hours.
Reasonable control of screen tension should pay attention to the consistency of screen thickness, uniformity of exposure, screen durability. Accurately adjust and control the screen distance, positioning, dimensional stability, ink consumption and energy consumption in the printing process. Attention should be paid to control the factors affecting the tension, and reasonable selection of tension equipment and method. Diazo photosensitive agent and photosensitive film are commonly used in plate photosensitive materials. Diazonium emulsion is widely used in screen printing. The photosensitive film has the characteristics of uniform and controllable film, high resolution, high wear resistance and strong adhesion with the screen. It has been widely used in character printing of printed board. It is necessary to pay attention to the thickness of the film. Generally, 25 μ M-30 μ m is recommended for solder mask printing, e 15 μ m-20 μ m for printed wire and character.
2) Printing of resist film
The design of the circuit group printed on the laminate to form an anti-corrosion film is completed by screen printing. There are two kinds of screen printing with anti-corrosion film. One is to use anti-corrosion ink to print the circuit part, that is, to print the anti-corrosion ink on the part that needs to keep the copper foil. In this way, the circuit part will be retained during corrosion to form a conductive circuit. Second, do not use anti-corrosion ink printed circuit, on the contrary to printed circuit outside the part. That is to make the parts outside the circuit have corrosion resistance. When the components are installed, the double-sided and multi-layer circuit boards are almost printed in this way.
Soldering tin or gold should be used for electroplating, and copper fluoroborate plating solution should be used for soldering tin. The ratio of tin to lead in soldering tin is 3:2. Weak acid solution is used for gold plating. The anti-corrosion ink film of electroplating must be able to withstand the corrosion of pretreatment solution and electroplating solution, and finally can be simply stripped. When electroplating the circuit, copper should be plated to a certain thickness first, and then the solder is plated on it. The thickness of electroplating is 30 μ m for copper, 10 μ m for solder and 25 μ m for gold. After electroplating, the anti-corrosion film is peeled off by using ink remover and soft brush.
3) Solder mask printing
The printed circuit board that has been cleaned after etching should be screen printed with solder mask immediately. The solder mask ink is applied to the printed circuit board. However, the process parameters of different screen printing machines are different. Generally speaking, the printing speed is controlled at 100mm/s – 150 millimetro / s, the screen printing pressure is 4.0kg/c㎡ – 6.0kg/c㎡, the blade hardness is 65 degrees, the blade angle is 65 degrees – 70 degrees, the number of scrapers is 1 / face – 2 / surface, and the screen distance is 4 millimetro – 8 millimetro. Before screen printing, it is necessary to incline the screen printing machine shell and worktable surface. Before printing the first plate, it is necessary to clean the screen surface with cots and try printing several times with white paper. Generally, the worktable needs to be cleaned every two hours. Before the formal screen printing, a trial printing board must be carried out, and the quality of the printing plate should be checked to ensure that the printing oil is uniform and the thickness is consistent, and there is no phenomenon of poor oil or oil entering the hole, no garbage and dust, and so on. The screen printed plate must be placed on the plate frame at intervals, and can be pre baked in the oven after 10 to 15 minutes.
In screen printing, pay attention to control the thickness of solder mask. The scrapped solder mask plate printed with solder mask can be selected, and the product code, batch number and type of solder mask used shall be indicated in the specified report. Then, according to the requirements of different parts of the sample to be tested, with a special hand plate for metallographic section blanking. The thickness of solder mask on both sides of the line should not be less than 5 μ m, and the thickness of solder mask in the middle of the line should not be less than 10 μ M. The pencil hardness should reach 6h-7h. If the film surface is sticky, it means that the curing time is insufficient or the film is too thick. The curing time or film layer can be appropriately extended.